鎢細泥製備鎢酸鈉
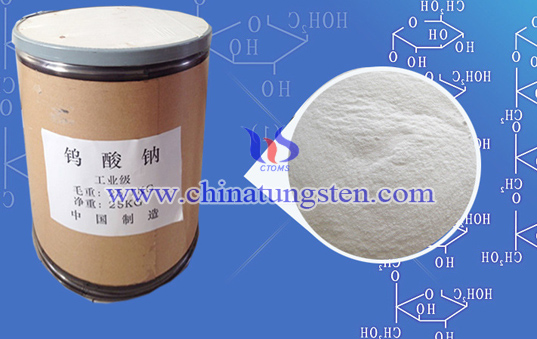
一、前言
鎢酸鈉和仲鎢酸按為重要的化工原料及鎢冶金生產中的重要中間產品。目前,國內工業上生產高純鎢酸鈉主要是用鎢精礦作原料,因此生產成本較高。這在當前的市場情況下將嚴重虧損。我國南方各省鎢選廠在選出鎢精礦的同時,產出部分鎢細泥,按WO3量計其價格僅為精礦價格的60-70%,即按WO3計每噸價格要少7000-8000元。因此,利用這種價廉的原料生產鎢酸鈉和仲鎢酸錢是降低成本的有效方法。
鎢細泥的特點是高鈣、高雜質、低品位。如用經典法處理,不僅分解率低(如處理含Ca為3%的原料,分解率一般只有90%左右),而且產品中雜質含量很高。鑒於熱球磨堿分解技術對高鈣低品位礦有很強的適應能力,同時具有較強的抑制雜質的效果,以及新開發出離子交換法從鎢酸鹽洛液寧除鋁的技術,能從含鋁量高的鎢酸鹽溶液中深度除鑰,鎢的回收率高。因此,將上述方法組成一個用高鈣高雜質鎢細泥為原派書硯取高純鎢酸呐和高純仲鎢酸按的新工藝,用於化工廠的工業生產中。
在上述流程中,第一步是利用堿法熱球磨使鎢細泥分解,將大部分雜質抑制在渣中,達到使WO3轉入溶液而絕大部分雜質(P, As,Si等)留在渣中的目的。
第二步是將得到的粗鎢酸鈉溶液進行一次蒸發結晶,以回收堿並除去部分P, As,Si等雜質。
第三步是將鎢酸鈉晶體進行溶解過濾得到鎢酸鈉溶液,一方面用離子交換法進行鎢鋁分離,再經二次蒸發結晶得到高純鎢酸鈉產品;另一方面可將該鎢酸鈉溶液經離子交換法轉型為鎢酸按溶液,再經離子交換法除鑰,然後蒸發結晶得到高純仲鎢酸按。
二、堿法熱球磨分解
1.原料和設備。小型試驗和工業試驗分別在體積3.75L和1M3的熱磨反應器內進行,每次處理礦量分別為300g(小試)和600kg(工業試驗)。
2.試驗結果。在小試條件下l,對礦1,在堿用量為理論量的3.0-3.5倍,160℃下分解1.5小時,鎢分解率平均達97.74%。P,As, Si等幾種主要雜質的平均浸出率分別為4.73%,4.05%和1.98%。對礦3;鎢的平均分解率為99%,雜質P,As,Si的平均浸出率分別為3.18%,0.49%和2.69%。在工業試驗中,鎢的平均分解率為96.92%,雜質P, As, Si的浸出率和,小試結果相一致。
用本工藝處理高鈣高雜質鎢細泥,所得到的鎢酸鈉溶液的品質基本上達到經典法處理黑鎢精礦的水準,因此,用堿法熱球磨分解高鈣高雜質鎢細泥,不僅保證了高的鎢分解率,並且抑制了雜質的浸出,保證了鎢酸鈉溶液的品質,這為利用廉價高鈣高雜質中礦,生產合格產品創造了條件。
三、鴿酸鈉溶液的濃縮結晶
為進行鎢堿分離,並進一步除雜,將分解得到的粗鎢酸鈉溶液進行了蒸發結晶。試驗結果表明NaOH 98%以上可返回利用。73.1%的P, 95.38%的As, 95.19%的Si亦進入返回液,與鎢分離。實踐證明,這種返回液中的雜質在分解過程中進入渣,不造成雜質的積累,而Na2WO4•2H2O晶體中的P/WO3, As/WO3值已接近或超過傳統工藝淨化鎢酸鈉溶液得到合格APT的要求,但Mo/WO3仍高。
四、離子交換分離鉑
鎢細泥中含鋁較高,Mo/WO3達0.5-0.6%,分解得到的鎢酸鈉溶液中Mo/ WO3高達0.13-0.19%。為了生產高純鎢酸鈉和APT,必須從鎢酸鹽溶液中除鋁。
目前在鎢冶煉中從鎢酸鹽溶液中除鋁的方法有兒種,但每種方法都存在某些缺點。尤其是對鋁含量高的鎢酸鹽溶液,不是難以達到除鋁要求,就是鎢回收率太低。本研究是用離子交換法從鎢酸鹽溶鹽中除鋁。
從上述試驗結果可看出,離子交換法可以從鎢酸鹽治液弓深度除鋁,鎢的回收率高,操作簡易,元廢渣和有害氣體產生。
五、結論
1.本工藝根據鎢細泥低品位、高鈣(Ca 7%)、高雜質含量的特點,採用具有國內外先進水準的技術,如熱球著分解並抑制雜質,離子交換法除鋁等組合而成,生產高純鎢酸鈉和APT,全流程組合含理,具有流程短,回收率高,產品純度高等特點。
2,本工藝有效地利用了我國的高鈣高雜質鎢細泥資源,擴大了資源的利用率。成本低,根據四圈化工廠1992年統計,高純鎢酸鈉的生產成本,僅為某廠按傳統法處理黑鎢精礦生產同類產品的71%。每噸APT產品可獲純利5800元。因此,有著不可估量的社會效益和明顯的經濟效益。
3.本工藝對三廢處理較好。生產鎢酸鈉時,全流程屬閉路迴圈,各種有害雜質(如P、As、Si等)固定在渣中。生產APT時,僅少部分有害雜質進入交後液及結晶母液的處理後液,可按傳統方法得到有效處理,絕大部分有害雜質亦進入渣中。